Welding is a crucial skill in various industries, from construction to automotive repair. Whether you’re a professional welder or a DIY enthusiast, having the right welding machine can make all the difference in the quality and efficiency of your work. In this comprehensive guide, we’ll explore the different types of welding machines, their applications, and key factors to consider before making a purchase.
Types of Welding Machines
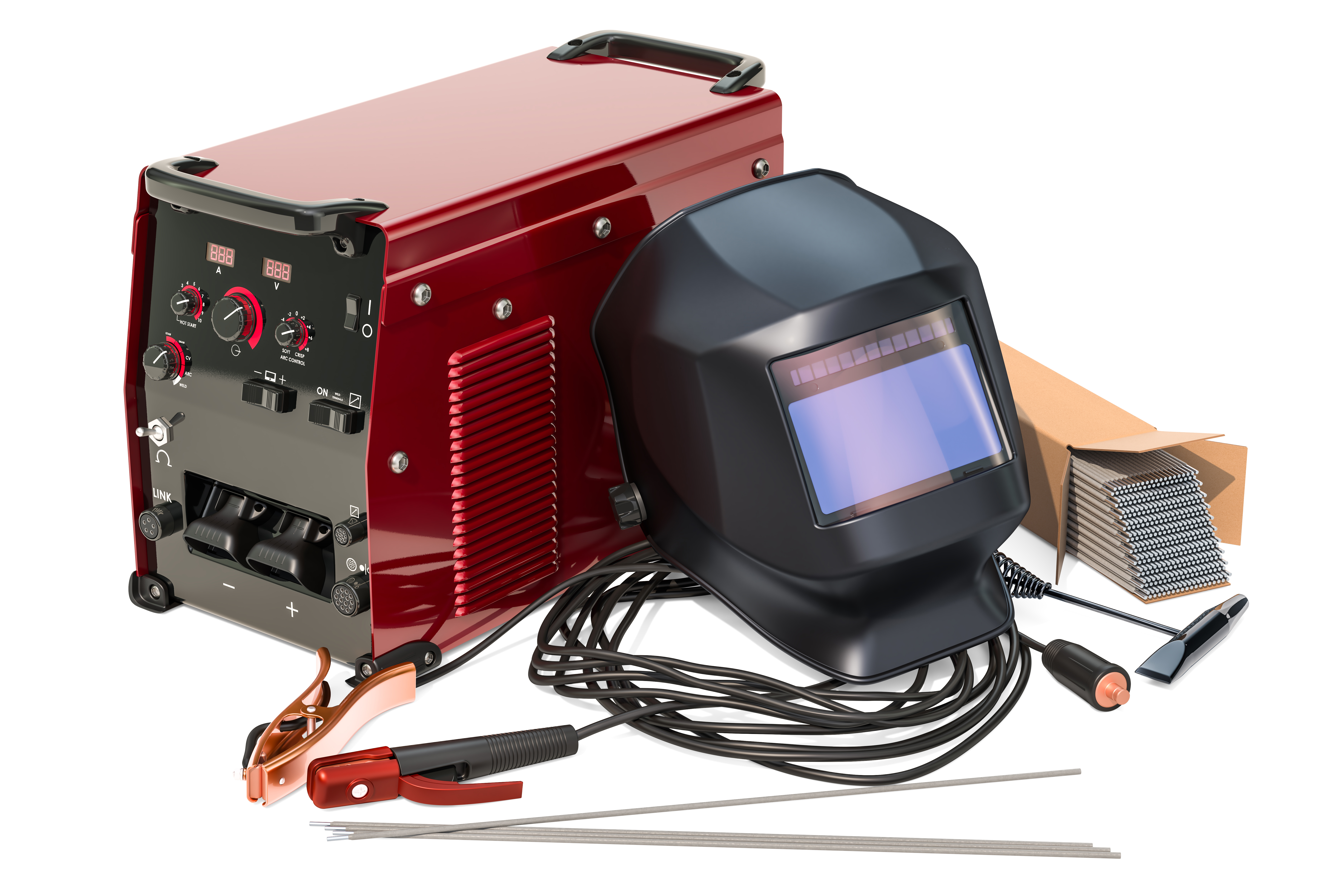
1. MIG Welding Machines (Metal Inert Gas)
MIG welders are popular for their ease of use and versatility. They use a wire electrode fed through a welding gun, making them ideal for beginners and professionals alike. These welding machines are perfect for automotive repairs, fabrication, and home projects.
Pros:
- Fast welding speed
- Clean and precise welds
- Suitable for thin and thick metals
Cons:
- Requires shielding gas
- Not ideal for outdoor use due to wind interference
2. TIG Welding Machines (Tungsten Inert Gas)
TIG welders offer superior precision and are commonly used for high-quality welds on stainless steel, aluminum, and other non-ferrous metals. These welding machines are favored in aerospace, automotive, and artistic welding.
Pros:
- Produces high-quality, clean welds
- Works on a wide range of metals
- Greater control over the welding process
Cons:
- Steeper learning curve
- Slower than MIG welding
3. Stick Welding Machines (Shielded Metal Arc Welding – SMAW)
Stick welders are rugged and reliable, making them ideal for outdoor and heavy-duty welding. These welding machines are commonly used in construction, pipeline welding, and repair work.
Pros:
- Works well on rusty or dirty metals
- No need for shielding gas
- Portable and durable
Cons:
- Produces more spatter
- Requires frequent electrode changes
4. Flux-Cored Welding Machines
Similar to MIG welding, flux-cored welders use a tubular wire filled with flux instead of shielding gas. These welding machines are excellent for outdoor welding and heavy fabrication.
Pros:
- No shielding gas required
- High deposition rates
- Works well in windy conditions
Cons:
- Produces more smoke and fumes
- Not ideal for thin metals
Key Factors to Consider When Choosing a Welding Machine
1. Power Requirements
- 110V vs. 220V: Smaller welding machines run on 110V, making them suitable for home use, while industrial-grade machines require 220V for higher power output.
- Duty Cycle: Indicates how long a welder can operate before overheating. A higher duty cycle (e.g., 60%) means longer continuous use.
2. Material Thickness
Different welding machines handle varying metal thicknesses. For thin metals (e.g., sheet metal), a MIG or TIG welder is ideal. For thicker materials, a stick or flux-cored welder works best.
3. Portability
If you need to move your welder frequently, consider a compact, lightweight model. Inverter-based welding machines are more portable than transformer-based ones.
4. Budget
Prices vary based on features and capabilities. Entry-level MIG welders start around 300,whileindustrial−gradeTIGwelderscanexceed2000.
5. Ease of Use
Beginners should opt for MIG or flux-cored welders, while experienced welders may prefer TIG or stick welding for greater control.
Top Applications of Welding Machines
- Automotive Repairs: Fixing exhaust systems, body panels, and frames.
- Construction: Building structures, pipelines, and heavy equipment.
- Manufacturing: Fabricating metal parts and machinery.
- DIY Projects: Creating custom furniture, gates, and artwork.
Maintenance Tips for Your Welding Machine
To ensure longevity and optimal performance:
- Clean Regularly: Remove dust and metal debris.
- Check Connections: Loose cables can affect performance.
- Replace Consumables: Electrodes, nozzles, and liners wear out over time.
- Store Properly: Keep in a dry, dust-free environment.
Conclusion
Choosing the right welding machine depends on your project needs, skill level, and budget. Whether you need a MIG welder for quick repairs or a TIG welder for precision work, understanding the differences will help you make an informed decision. Investing in a high-quality welding machine ensures strong, durable welds and enhances your productivity.
By considering power requirements, material thickness, and portability, you can find the perfect welding machine for your workshop. Happy welding!