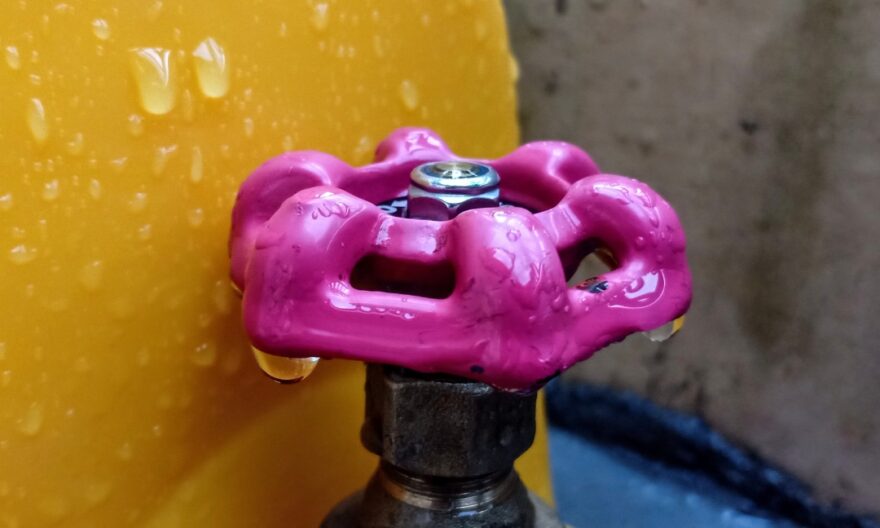
Gate valves are frequently employed in industrial settings to regulate the flow of different liquids, gases, and slurries. To let or prevent flow, these valves operate by raising and lowering a gate or wedge. In addition to their many benefits, gate valves have a few drawbacks to consider before choosing them for a certain application.
Advantages of Gate Valves:
1. High Flow Capacity
The large flow capacity of gate valves is one of its main features. Gate valves have a straight-through flow passage, and when the valve is fully opened, the gate or wedge is completely removed from the flow stream. As a result, the pressure drop across the valve is kept to a minimum, enabling optimum flow capacity. Gate valves are, therefore, perfect for uses that call for large flow rates. Because they can manage large flow rates with little pressure loss, gate valves are frequently the valve of choice in sectors including oil and gas, water treatment, and chemical processing. This makes them an effective and affordable option.
2. Tight Sealing
The excellent sealing properties of gate valves are another benefit. The gate or wedge must be entirely closed to stop any fluid from going through. At that point, it creates a tight seal with the valve body. Gate valves are the best choice for applications that demand high isolation. In situations where leakage cannot be permitted, including in chemical processing, oil and gas production, and water treatment facilities, gate valves are frequently utilised. Gate valves are appropriate for high-pressure applications because of the tight sealing.
3. Low-Pressure Drop
Another benefit of employing gate valves in diverse applications is that they have a minimal pressure drop. The valve’s gate or wedge entirely exits the flow passage when fully opened, minimising the flow restriction. The system can sustain high flow rates with less energy input due to the lower pressure drop across the valve. This makes gate valves the perfect option for systems that need efficient flow rates, particularly in high-pressure situations where energy consumption is a major concern. Gate valves are a common option in various sectors because of their low-pressure drop characteristic, which also helps preserve energy, lower operating costs, and increase system efficiency.
4. Easy to Operate:
Gate valves have the additional benefit of being simple to use. Their simplicity and lack of numerous moving components make them simple to operate and maintain. The valve’s gate or wedge can easily open and close since it may move up and down. Additionally, gate valves are easy to open and close, making them perfect for use when the valve has to be opened and closed repeatedly. Because it is so simple to use, there is less chance of operator mistakes and weariness, making the workplace safer.
Disadvantages of Gate Valves:
1. Slow to Open and Close
Gate valves’ sluggish opening and closing times compared to other valve types are one of their main drawbacks. To fully open or close the valve, the gate or wedge must be pushed a fair distance, which might take some time. This sluggish functioning may be a disadvantage in applications where a quick reaction is necessary, such as emergency shutdown scenarios. Gate valves may also not be appropriate for applications requiring frequent operation due to the sluggish operation’s potential for delays or inefficiency. Despite this restriction, gate valves are a common option for situations that need a dependable and effective valve solution.
2. Susceptible to Clogging:
The potential for clogging with gate valves is still another drawback. The design of gate valves makes it possible for the wedge or gate to catch dirt or other particles in the flow channel. This may result in the valve clogging up over time, reducing flow rates, or causing the valve to fail. In situations where the fluid being conveyed contains particulates or debris, gate valves in particular, this is particularly true. Regular maintenance and cleaning are crucial to reduce the possibility of blockage. Other valve types, including ball or butterfly valves, could be better when clogging is a serious problem.
3. Limited Throttling Capabilities
Butterfly valve also has limited throttling capabilities, which is a significant disadvantage. Due to their construction, gate valves are generally intended for full-open or full-closed operations. They are, therefore, inappropriate for applications requiring fine flow control or throttling. Gate valves may be damaged if used for throttling operations, which shortens their lifespan and causes early wear. Other valve types, such as globe or needle valves, offer a more suitable option in situations that call for precise flow control or throttling. Despite this drawback, gate valves are a common option for applications that demand dependable, full-open or full-closed valve operations.
4. High Cost:
A disadvantage of gate valves is their comparatively high price compared to other valve types. Because of their intricate design and expensive materials, gate valves are often more expensive than ball or globe valves. Gate valves also need more upkeep and cleaning than other valve types, which can raise the overall cost. Gate valves are only some of the most cost-effective solutions where the price is the key consideration. However, the advantages of gate valves could offset the extra expense in applications that need a dependable and effective valve solution. The best valve type may be chosen if the needs of the application and the available budget are carefully considered. We also provide Butterfly valve.
What are the Applications of Gate Valves?
The capacity of gate valves to handle high-pressure and high-temperature applications makes them a common component in the oil and gas sector. They are frequently employed in upstream, midstream, and downstream operations, such as oil and gas production, transportation, and exploration. The flow of gas and oil from wells is controlled in upstream operations using gate valves. Gate valves are employed in midstream operations to regulate the movement of gas and oil via pipelines. Gate valves are used in downstream processes to regulate the flow of oil and gas into refineries and chemical plants. Gate valves are also employed in building offshore platforms, where they must survive corrosive environments and erosive conditions while being exposed to extreme environmental conditions.
Gate valves are employed in manufacturing, processing, and handling chemicals in the chemical industry. They are frequently employed in producing corrosive materials like acids, alkalis, and other compounds. Gate valves are also employed in transporting chemicals, including the movement of gases and liquids between various phases of the production process. Gate valves are a great option for situations where the environment and personnel might be seriously endangered by releasing dangerous substances due to their tight sealing capabilities.
Final Talk
Gate valves have many advantages that make them ideal for certain applications. Their high flow capacity, tight sealing capabilities, low-pressure drop, and ease of operation make them popular in many industries. However, gate valves also have some disadvantages that need to be considered, such as their slow opening and closing time, susceptibility to clogging, limited throttling capabilities, and high cost. When selecting a valve for a particular application, it is important to consider both the advantages and disadvantages of gate valves and other valve types to choose the valve that best meets your needs.
Also check: Effective Acne Treatments to Clear Skin Ahead