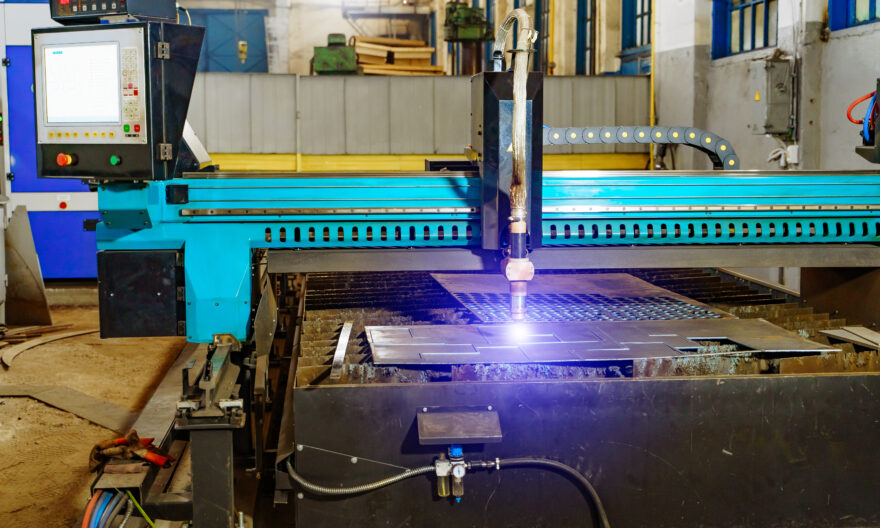
A plasma cutting machine is a powerful tool used in metal fabrication to cut through electrically conductive materials with precision and speed. Utilizing a high-velocity jet of ionized gas (plasma), these machines deliver clean, accurate cuts on steel, aluminum, brass, and other metals.
In this comprehensive guide, we’ll explore how a plasma cutting machine works, its key components, benefits, applications, and factors to consider when choosing the right one for your needs.
How Does a Plasma Cutting Machine Work?
A plasma cutting machine operates by generating an electric arc through a gas (such as nitrogen, oxygen, or argon), ionizing it into plasma. This superheated plasma melts the metal, while a high-speed gas stream blows away the molten material, resulting in a clean cut.
Key Components of a Plasma Cutter
-
Power Supply – Converts AC voltage into a stable DC current to sustain the plasma arc.
-
Plasma Torch – The handheld or automated tool that directs the plasma stream.
-
Gas Console – Regulates the flow of plasma and shielding gases.
-
CNC Controller (for automated systems) – Ensures precision cuts with computer-guided accuracy.
Advantages of Using a Plasma Cutting Machine
-
High Precision & Clean Cuts – Delivers smooth edges with minimal slag.
-
Fast Cutting Speeds – Cuts thicker metals quicker than traditional methods.
-
Versatility – Works on various conductive metals, including stainless steel and copper.
-
Cost-Effective – Lower operational costs compared to laser cutting.
-
Minimal Heat Distortion – Reduces warping in thin materials.
Applications of Plasma Cutting Machines
A plasma cutting machine is widely used across industries, including:
-
Automotive Manufacturing – For cutting exhaust systems and body panels.
-
Construction – Fabricating structural steel beams and metal frameworks.
-
Shipbuilding – Precision cutting of thick metal plates.
-
Art & Metal Sculpting – Creating intricate designs in metal artwork.
-
Industrial Repairs – Cutting and repairing heavy machinery components.
Types of Plasma Cutting Machines
-
Manual Plasma Cutters – Handheld torches ideal for small workshops.
-
Mechanized Plasma Cutters – Automated systems for industrial use.
-
CNC Plasma Cutters – Computer-controlled for high-precision cutting.
-
Hybrid Plasma-Laser Cutters – Combine plasma and laser technology for enhanced efficiency.
How to Choose the Right Plasma Cutting Machine
When selecting a plasma cutting machine, consider:
✅ Cutting Capacity – Match the machine’s amperage to your material thickness.
✅ Duty Cycle – Higher duty cycles allow longer continuous operation.
✅ Portability – Choose between benchtop or handheld models.
✅ Automation Level – CNC systems offer better accuracy for complex cuts.
✅ Gas Requirements – Some machines support multiple gases for different metals.
Maintenance Tips for Plasma Cutting Machines
To extend the lifespan of your plasma cutting machine:
✔ Clean the Torch Regularly – Remove spatter and debris.
✔ Inspect Consumables – Replace worn electrodes and nozzles.
✔ Check Gas Flow – Ensure proper pressure for optimal cuts.
✔ Lubricate Moving Parts – Prevent friction in mechanized systems.
Conclusion
A plasma cutting machine is an indispensable tool for metalworkers, offering speed, precision, and versatility. Whether for industrial fabrication or artistic metalwork, investing in the right plasma cutter can significantly enhance productivity and cut quality.
By understanding its working principles, benefits, and maintenance needs, you can maximize the efficiency of your plasma cutting machine and achieve flawless metal cuts every time.